
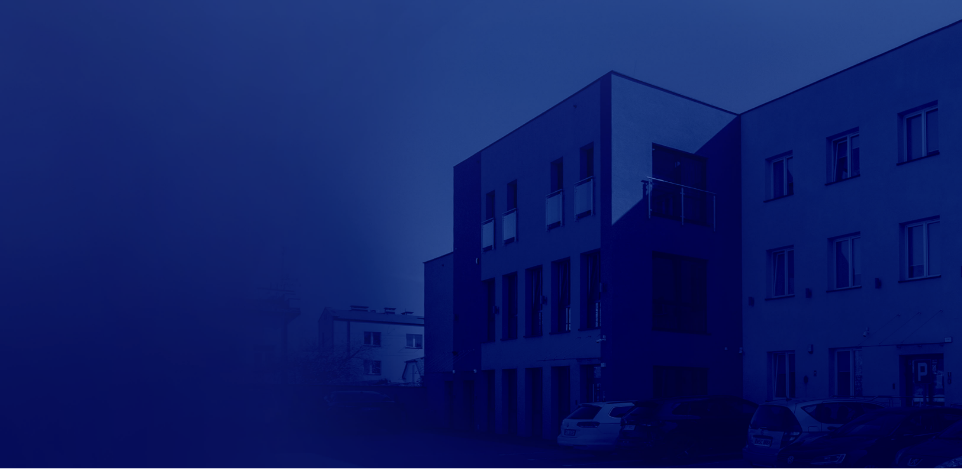
Warehouse Work: How to Increase Your Productivity?
Warehouse operations form one of the pillars of modern logistics and supply chain management, making efficiency in this area critical to the success of the entire business. However, warehouse productivity is not just about picking orders quickly or arranging goods on shelves in an orderly manner. Equally important are proper organization, effective time management, workplace safety, and seamless teamwork. Thanks to the development of new technologies, such as Warehouse Management Systems (WMS), barcode scanners, or automated storage systems, those responsible for warehouse organization can plan tasks and allocate resources more effectively. Unfortunately, even the best tools will not bring the desired results if you lack a well-coordinated and well-prepared team.
Why is this so important? High warehouse efficiency directly impacts operating costs, customer satisfaction, and ultimately a company’s financial performance. If warehouse processes are poorly organized, a company can waste time and resources, generating unnecessary expenses. On the other hand, a smooth flow and reliable inventory management significantly speed up order fulfillment, resulting in higher service levels, fewer errors, and greater trust from business partners.
The goal of this article is to comprehensively discuss ways to increase efficiency and productivity in the warehouse. We will focus on concrete, practical advice: starting with the basics of organization, moving on to key aspects of time management, technology, and occupational health and safety (OHS) rules, and finally addressing communication issues and building an effective team. We will try to explain how to minimize mistakes while continuously developing to meet the growing demands of the market. Thanks to this, you will understand which areas of everyday warehouse operations can be optimized to significantly improve both productivity and workplace safety.
We have also gathered tips on how to plan your personal skill development step by step—regardless of whether you have been working in the industry for years or are just starting out. Equally important will be a discussion of how the right tools or modern systems can relieve employees of the most time-consuming tasks. After all, a warehouse is a place where different people, equipment, and technologies must work closely together. If you want to find out how to optimize your work, reduce errors, and at the same time take care of safety and comfort, we invite you to read on.
Table of Contents
- Warehouse Work Organization and the Importance of Space Management
- The Use of Technology in the Warehouse
- OHS Rules and Safety Culture
- The Importance of Communication and Teamwork
- Time Management and Continuous Skill Development
Article Plan
- In the first part, we will focus on the key aspects of warehouse organization: from shelf arrangement to optimal zone labeling.
- Next, we will move on to modern technological solutions and show how they effectively support everyday work.
- The third section will discuss the importance of OHS rules as well as ways to build a culture of safety in the company.
- The fourth part will be devoted to communication and teamwork, which underpin the smooth flow of information and tasks.
- Finally, we will look at time management and continuous skill development.
Warehouse Work Organization and the Importance of Space Management
Properly planning the warehouse space is one of the foundations for the efficient operation of the entire logistics department. How products are laid out affects not only order-picking speed but also the frequency of errors. It is important to consider the characteristics of the stored goods—their dimensions, weight, susceptibility to damage, or temperature requirements. Properly placed shelves, clearly marked zones and aisles, and defined traffic routes significantly simplify work and reduce the time needed to handle each task. Both experienced warehouse managers and new employees increasingly notice that even small changes in layout can yield surprisingly large benefits in terms of reducing costs and working hours. However, organization does not only involve physical shelf arrangement; it also requires defining procedures and encouraging employees to follow established standards, which, in the long run, increases process stability and safety.
To ensure efficient and effective warehouse management, it is worth starting with the creation of a space map that includes receiving, storage, packing, and shipping zones. The ABC model is often employed, where the most popular products (so-called A items) are placed in the most accessible spots to reduce picking time. Less frequently rotating items (C) can be placed on higher shelves or in parts of the warehouse that are less trafficked. Labels with barcodes or QR codes can also be very helpful, speeding up the identification of products.
Procedures play a crucial role in organization. Develop clear instructions for receiving, quality checking, picking, and shipping goods. Create checklists so that employees can confirm at any time whether all the steps have been completed correctly. Remember that the warehouse is a place of teamwork — each member should feel responsible not only for their own station but also for the entire process. That is why constant communication and shared rule-setting are so important.
Best practices in organization can manifest in many ways: from clear, brightly colored markings of pathways and danger points, through regular clearing of aisles, to meticulously returning tools and equipment to their designated places. As a result, many collisions and hazardous situations can be avoided, and tasks can be carried out more quickly. If the warehouse is tidy and orderly, it is much easier to introduce improvements, including those of a technological nature.
The Use of Technology in the Warehouse
Today, it is hard to imagine a modern warehouse functioning without technological support. WMS (Warehouse Management Systems) allow real-time monitoring of stock levels and locations, planning the placement of individual products, and even generating efficiency reports. Portable barcode scanners have become extremely popular, as they greatly reduce the risk of errors when entering data. Automated storage racks, autonomous guided vehicles (AGVs), or robots supporting order picking are also becoming less a luxury and more a standard in larger companies that aim to improve productivity. All this means that human labor can be lighter, faster, and free of tedious, repetitive tasks, while the business itself gains a competitive advantage.
The key to effectively harnessing technology is choosing solutions appropriate to the warehouse’s needs. While large companies can afford advanced automation and robotics, smaller entities can benefit from simpler yet still effective solutions, such as RFID labels, modular mobile applications, or automated pallet trucks. It is also important to remember to properly train staff. Even the best tool will not improve productivity if employees do not know how to take full advantage of it.
Paper pick lists are increasingly being replaced by digital displays or pick-by-voice systems, which allow for hands-free order processing without having to pause packing. These solutions positively affect work efficiency and convenience, while also reducing the number of mistakes caused by illegible notes or lost documents. In the coming years, we can expect further development of Internet of Things (IoT) solutions and Artificial Intelligence (AI), which will enable precise, real-time data analysis and rapid response to potential issues.
In summary, warehouse technologies are not a passing trend but a necessity arising from growing market demands and continued pressure to reduce costs. With the proper implementation of IT and automation tools, the work of warehouse employees becomes easier, safer, and more efficient, directly impacting the company’s financial health.
OHS Rules and Safety Culture
Workplace safety is paramount, regardless of whether we are talking about large distribution centers or small local warehouses. The negative consequences of failing to follow OHS procedures can be devastating for both employees and the company. Accidents can lead to health issues, and in the worst cases even threaten lives. This entails high medical costs, work stoppages, and potential legal ramifications. In today’s rapidly growing logistics sector, with ever-increasing demands on warehouses, safety culture must be a top priority for every company. Maintaining productivity relies on each employee understanding their role in creating a safe work environment and having access to clear instructions for each task.
The first step is to establish and regularly update OHS documentation. It should include information on potential hazards, procedures to follow, and fundamental guidelines for using equipment. Providing employees with suitable personal protective equipment — such as helmets, reflective vests, and appropriate footwear, depending on the nature of the work and associated risks — is also crucial.
Education is equally important. Regular training sessions, briefings, and reinforcing safety principles — through posters or short reminders before the shift starts — keep employees vigilant. Remember that in a busy warehouse environment, routine and habit can quickly set in. That is why it is important to encourage the team to address improper behavior, even minor infractions, and to report any potential hazards.
Instilling a safety culture is not a one-time task but an ongoing process requiring the involvement of the entire team, including management. For example, managers and leaders should set an example — demonstrating that OHS rules are not just a formality but a real measure to protect employees and maintain an efficient warehouse. This approach increases not only safety but also the morale of the workforce.
The Importance of Communication and Teamwork
A warehouse is a place where successful teamwork is paramount. The division of responsibilities, coordination of activities, and rapid response to immediate needs are only possible when open, efficient, and clear communication is in place. Two levels of interaction overlap here: communication within the warehouse team and communication with other company departments (e.g., purchasing, sales, or transport). From the warehouse worker’s perspective, direct and quick information exchange with colleagues helps avoid misunderstandings, streamlines operations, and boosts motivation and trust within the team. Meanwhile, proper communication with other departments ensures that orders, shipping preparations, or handling of returns occur without unnecessary delays or confusion.
Several elements contribute to efficient communication. First, make sure instructions — written and verbal — are clear. This way, everyone knows exactly what they should be doing and how. Second, consider holding team meetings to summarize results, present plans for the coming days, and discuss current issues. These meetings are also useful for sharing ideas on improving operations and boosting team morale.
Another aspect is the use of communication tools. Even in a warehouse, information boards or shelves labeled “Tasks for Today” can greatly simplify work organization. In large warehouses, it is common to use systems that collect reports from employees and assign them to the right people. Fast and clear information flow helps identify bottlenecks, minimize errors, and respond more effectively to sudden changes, such as unexpected delivery schedules.
One should also remember to foster trust and mutual support. A team that values open discussion and mutual help is much better equipped to handle unplanned challenges. Even the most advanced tools cannot replace the human element of goodwill among colleagues. Communication becomes the glue that binds all elements of the warehouse process into a harmonious whole.
Time Management and Continuous Skill Development
Time management is one of the most important professional skills today, and it is particularly crucial for warehouse work. Teams that use appropriate planning and prioritization methods can truly increase their productivity, avoiding chaos and unnecessary downtime. In the rapidly evolving logistics sector, effective task management and the ability to adapt to frequent changes in orders, delivery deadlines, or unexpected equipment malfunctions can determine whether a warehouse thrives or struggles. Another important factor is employee skill development — from forklift operator courses and WMS system training to soft skills training in communication, which improve the working atmosphere and information flow within the team.
The foundation of good time management is establishing priorities. Large orders or the most urgent shipments should be handled first to minimize delays and improve the company’s reputation in the eyes of customers. Keep in mind the need for flexibility — not everything can be predicted, so plans should include a buffer for unforeseen events.
As for continuous skill development, it is valuable to encourage employees to participate in training sessions, share experiences, and take advantage of external courses. This not only promotes individual professional growth but also boosts the overall productivity of the warehouse. A well-thought-out motivation system is also important, rewarding initiative and the active pursuit of improvements. This might include making small process changes that save time — for example, through better organization of goods or more effective use of IT tools.
It is also worth mentioning the role of rest and recovery. Teams that work under excessive stress without sufficient time to relax make more mistakes and are less motivated to implement improvements. Hence, taking into account ergonomics and health aspects of the job, organizing breaks, or rotating staff in more physically demanding positions is crucial. Taking care of people is taking care of the warehouse’s most important resource — a well-trained and willing workforce.
Summary
Working in a warehouse is much more complex than just moving goods from one place to another. To improve warehouse productivity, you need a comprehensive approach that covers organizing space and processes as well as consistently investing in employee development and safety. Proper warehouse organization and clear zone labeling help avoid confusion; modern technological tools speed up daily operations; OHS rules protect health and lives, and good team communication creates synergy among all parts of the process. Time management is also essential, becoming one of the key factors for success in the logistics industry. Regular training, knowledge sharing, and a positive work environment motivate employees to engage in initiatives that enhance the entire warehouse’s operations. By adopting the solutions described here, a company not only increases its efficiency but also becomes a more attractive place to work.