
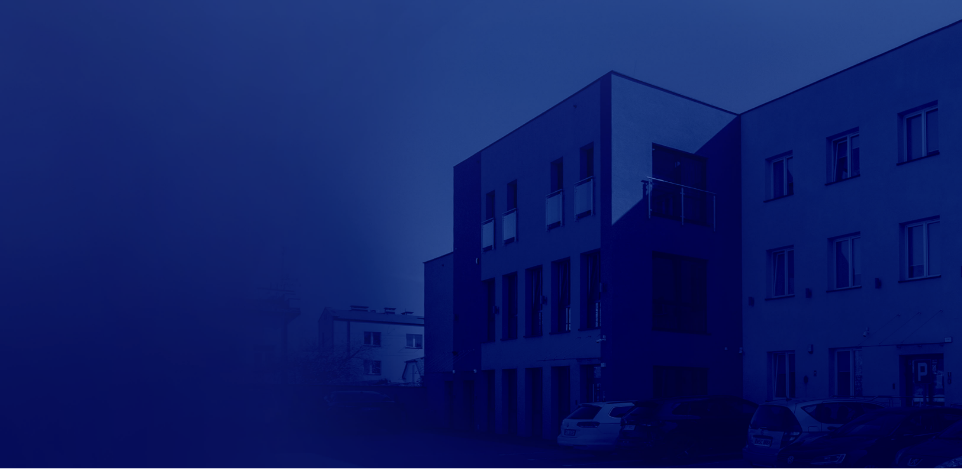
Warehouse Technologies: Automation and Its Impact on Employees
The automation of warehouse processes is becoming increasingly prevalent in companies worldwide. In an era of dynamic economic changes and growing competition, businesses are seeking ways to accelerate and streamline logistics operations, leading to the broader implementation of innovative technological solutions. Warehouse Management Systems (WMS), robots that support order picking and goods transfer, or automated sorting machines are just some of the tools that were considered novel only a few years ago but are now becoming the standard in many industries. This process is unavoidable, as customer expectations for speed and accuracy of deliveries are constantly growing, forcing companies to continuously optimize their processes. Unfortunately, a rise in automation not only brings positive aspects such as faster operations and cost reduction but also raises questions about employees’ future: what qualifications will be required to operate and oversee new devices? Will people be completely replaced by robots, and if so – what does that mean for long-term professional development in warehouses?
For a long time, there has been debate about how the advancement of machines may transform the job market. Warehouses are characterized by repetitive and often physically demanding work, so automation appears to be a particularly promising direction for investment. Robots can work more efficiently and with fewer errors stemming from human fatigue. Of course, introducing technology involves costs and the necessity for training, which requires both time and financial resources. However, it is worth remembering that although technology is extremely promising, it is not a cure-all, and its implementation can require an appropriate organizational culture as well as employee flexibility. This article will showcase the latest technological solutions in warehouses, discuss their significance for improving efficiency and quality of logistics processes, and analyze the impact of automation on employees. We will examine aspects related to adapting to new conditions, acquiring new skills, and addressing concerns that humans may eventually become redundant as machines develop rapidly. We will also answer questions about training and career development in this new, automated reality.
Understanding these processes is particularly important for companies that are already deciding to implement advanced inventory and logistics management systems. In the context of content optimization (SEO), some of the key keywords to pay attention to are warehouse automation, robots in logistics, career development in warehouses, WMS systems, or automatic sorting. Not only do these phrases help reach people interested in the topic, but they also point to the directions in which the warehouse industry is evolving. In the following sections of the article, we will present detailed information about the most popular technological solutions, as well as their impact on efficiency and work organization in warehouses.
Table of Contents
- Section 1: Modern Warehouse Technologies – An Overview of Solutions
- Section 2: The Impact of Automation on Employees – New Responsibilities and Skills
- Section 3: Training and Support for Adapting to Changes
- Summary
Article Plan
- Section 1: A discussion of key technologies used in warehouses, such as WMS, robots, and automatic sorting systems. An explanation of why they are so important for optimizing logistics processes.
- Section 2: An analysis of how automation affects employees—how their scope of duties changes, which new skills they need, and how they can develop.
- Section 3: A discussion of the role of training and support in the process of implementing new technologies. Attention to potential concerns and ways to minimize them.
- Summary: A concise overview of the key information covered in the article and conclusions about further developments in warehouse automation.
Modern Warehouse Technologies – An Overview of Solutions
Modern warehouse technologies are not limited to simple machines performing tedious, repetitive tasks. We are now dealing with an entire ecosystem of solutions that complement one another and offer maximum efficiency gains. On one hand, there is software for managing resources and processes; on the other, advanced machines and robots that work alongside employees or completely take over certain stages in the supply chain. A deeper analysis of these solutions shows that implementing technology is not just a matter of purchasing equipment but also a careful process of integration with existing infrastructure. The aspect of security is also significant, both in terms of data (cloud data storage, protection against hacking) and physical safety (robots or automated systems collaborating directly with humans).
Leading among the most widely used technologies in warehouses today are WMS (Warehouse Management Systems). These are tools designed for comprehensive management of goods movement in the warehouse — from receiving deliveries, to monitoring stock levels and locations, through to organizing shipments. A WMS not only enables real-time inventory tracking but also the automatic planning and optimization of processes such as order picking or packing. This type of software can be fully integrated with other company systems, for instance, HR management tools or e-commerce platforms, allowing a complete synchronization of logistics activities.
Another critical element in future warehouses involves robots and automation. Modern robots can pick orders, move goods between shelves, and even control product quality. Thanks to sensors and advanced algorithms, they can effectively avoid obstacles and collaborate with humans on the warehouse floor. The typical benefits include higher efficiency, fewer errors, and the ability to operate continuously 24/7, which greatly speeds up customer service in many industries. Automatic sorting is an especially interesting part of automation — machines can recognize product types, direct them to the right warehouse zones, and prepare them for subsequent transport stages. For companies in the e-commerce or courier sectors, this significantly boosts the handling of bulk orders.
When talking about modern technologies, one should also mention digitizing the inventory process. Scanners and RFID (Radio Frequency Identification) enable rapid identification of product location and quantity, minimizing errors and streamlining employees’ work. By using such solutions, companies can synchronize the gathered data with CRM, ERP, or WMS systems to obtain a complete, always up-to-date overview of warehouse status.
Ultimately, the success of implementing these technologies depends on tailoring them to the specific needs of a given business, as well as the degree to which employees are prepared to work effectively with machines and software. Understanding the interdependencies among these various solutions and recognizing challenges such as system integration or data security is the foundation for a responsible approach to warehouse automation.
The Impact of Automation on Employees – New Responsibilities and Skills
Although warehouse automation brings many benefits in terms of process acceleration and lower operational costs, it significantly affects the workforce. Many people associate automation primarily with the threat of job loss, often sparking valid concerns and uncertainty about the future. However, the experience of companies that have already implemented modern technologies in their warehouses paints a different picture — employees often move on to more demanding tasks, undergo additional training, and become operators of advanced machines or coordinators of logistics processes. Thus, the change does not only mean replacing people with robots, but also evolving skill sets and broadening responsibilities.
It is essential to consider automation not just from a cost and profit perspective but also a human one. New technologies encourage the acquisition of new competencies and technical knowledge, which in turn can contribute to professional growth and greater job satisfaction. At the same time, it is important not to forget about employees who may struggle to adapt to the new environment. Hence, planning a transparent implementation strategy that includes support (for example, via training or mentoring) is crucial. Companies that successfully support their employees through such transitions typically see a double benefit: not only higher process efficiency but also a stable and engaged workforce.
Primarily, the nature of a warehouse worker’s job changes due to automation. Tasks that once involved manually moving loads or scanning items may be taken over by robots and intelligent lines. As a result, employees step into roles as operators, inspectors, or coordinators of automated lines. Often, this requires knowledge of computer operation, control systems, or basic process engineering. For some, it is a challenge; for others — a career development opportunity that seemed out of reach for warehouse work just a short time ago.
At the same time, the growing presence of automated warehouses increases the demand for specialists in machine and equipment maintenance. Employees who can maintain software (e.g., WMS, ERP systems) and hardware (sensors, robots, conveyors) are highly valued. This is why companies are more and more willing to invest in internal training programs to “grow” a workforce equipped with the right competencies. In this context, the keyword career development in warehouses takes on particular significance: automation creates new career paths that go far beyond traditional manual labor.
It should also be noted that the role of managers and team leaders in the warehouse is changing. Where it used to be crucial to oversee large groups of workers, it is now just as important to monitor goods flow indicators, analyze machine performance, and optimize processes with the help of data generated by WMS or other platforms. Managers who can skillfully combine soft skills with logistics and technology expertise become pillars of a well-functioning modern warehouse. A common thread in all these activities is the need for ongoing education and the updating of knowledge, especially given how rapidly technology can advance.
It is worth emphasizing that automation does not always mean drastic staff reductions. In some cases, it can even lead to higher employment — particularly in areas like quality control, infrastructure maintenance, or tasks requiring flexibility in addressing system anomalies. The key lies in a suitable implementation strategy that takes into account employee communication, clearly defined career paths, and the provision of necessary training.
Training and Support for Adapting to Changes
Introducing modern technologies into warehouses can be a complex, multifaceted process. On the one hand, there are advanced tools such as WMS or robots that require implementation, configuration, and ongoing maintenance. On the other hand, people are needed to operate these technologies and utilize their potential in daily work. Without adequate support, in the form of training and additional instructions, even the best equipment and the most sophisticated software will fail to deliver actual business benefits. Moreover, lacking proper workforce preparation can lead to resistance to change, decreased engagement, or, in extreme cases, protests or resignations. Therefore, to achieve the expected results from automation, the human factor cannot be ignored.
Another crucial aspect is matching the training format to the employees’ needs. Some will more easily absorb theoretical knowledge during lectures, while others will prefer practical workshops where they can test new solutions in a realistic environment. Collaboration with technology providers and external training companies with the necessary know-how can be vital. Implementing new systems or machines is not a one-off task but often a months-long project, where various departments — from IT to HR — must work together so unexpected problems do not hinder the process.
In practice, the training process can encompass several stages. The first step is often to assess needs and identify competency gaps. Do employees have the required basic technical or logistics knowledge? Can they operate electronic devices and understand the fundamentals of warehouse systems? Answers to these questions make it possible to prepare a personalized training program that genuinely addresses the workforce’s needs.
Next comes the stage of workshops and hands-on training, where employees can “get to know” the new equipment and see how they handle real-life scenarios. Activities like job shadowing (observing more experienced colleagues) or simulations of potential issues are invaluable in familiarizing personnel with day-to-day operations. Training typically concludes with an exam or certification, which motivates participants to thoroughly learn the material. Implementing a system of rewards and recognition for progress also boosts motivation and enhances the sense of security.
The following phase involves long-term support, which includes access to online training materials, dedicated helplines, and opportunities for regular consultations with experts. Such a structure prevents situations where employees are left alone with difficulties — a scenario that could reduce productivity or cause system failures. Indeed, automation does not end once a robot is purchased or a WMS is installed; it is an ongoing process that needs regular updates, monitoring, and fine-tuning.
Unquestionably, communication is also vital. Good information flow between managers and warehouse teams helps to avoid conflicts and misunderstandings. Employees must clearly understand the company’s goals for automation, how their day-to-day work will change, and what support they can expect from management. Only then will automation not be perceived as a threat but rather as an opportunity to enhance processes and develop professionally.
Summary
Warehouse automation and the new technologies that come with it, such as WMS, robots, or automatic sorting, represent both a response to increasing market demands and a catalyst for growth in the logistics sector. On the one hand, they bring tangible benefits to companies in the form of greater efficiency and accuracy; on the other, they require employees to be ready for continuous learning and adapting to a rapidly changing environment. Implementing cutting-edge hardware and software solutions does not have to mean widespread job losses — more often, it leads to changes in job nature and the creation of new positions related to operating and maintaining these technologies.
A strategic approach to implementation — one that includes training and support for staff, and recognizes that automation is a multi-stage process involving the entire organization — is crucial to success in this field. Responsible companies understand that investing in employee development is worthwhile because fully leveraging the potential of modern solutions depends on them. Ultimately, everyone wins: businesses optimize logistics processes, customers receive faster and more reliable service, and employees gain new skills and expanded career paths.
As technology evolves, the future of warehouses looks increasingly promising. Although automation may seem like a challenge for some, it is becoming the norm in the global economy, and its effects are already visible in many markets. Companies that invest in this area early and prudently will not only gain a competitive edge but also build higher quality relationships with their workforce — founded on human-machine collaboration rather than attempting to replace one with the other.